penguの事例
角一化成株式会社
データ化が
顧客との信頼をつなぎ、
工場の活気を生み出す
プラスチック及びゴム成形製品の製造販売を行なう角一化成様の滋賀事業所では、大手自動車メーカーからの発注を受け、大型2色成形品やコンソールボックスの製造を主に行なっています。昨今のものづくりの現場における人材不足や、デジタルデータ化の流れを踏まえ、penguを導入。従来は手入力していた作業日報をSUISUIOCR/SUISUIETLを活用することで、工場のDX化が大きく前進しました。他業務や他工場への展開も見据えた自動化による取り組みを紹介します。
- 業種:
- 化学
- 事業規模:
- 140名
- 部門:
- 生産管理部門
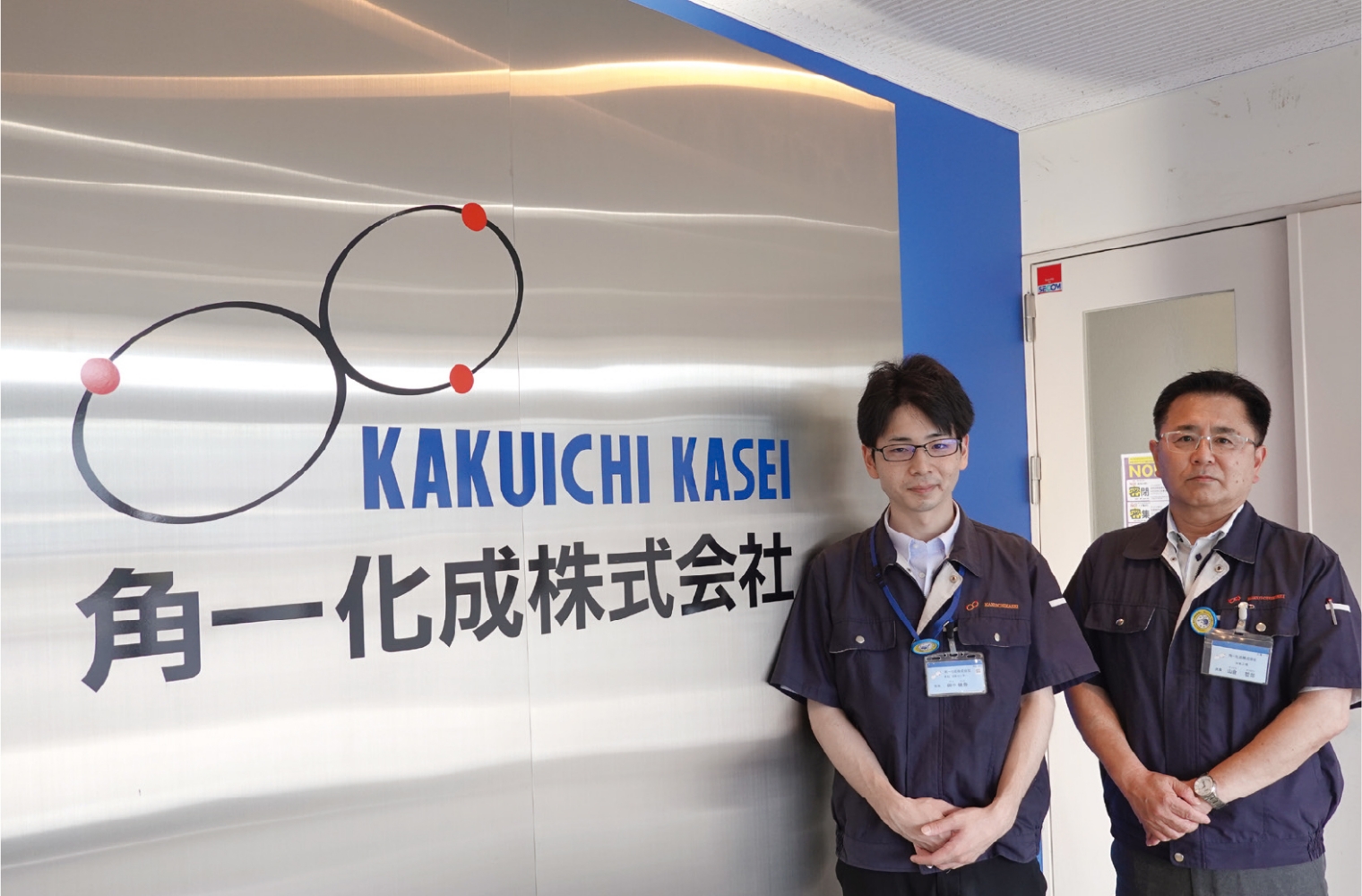
課題
- 生産管理の人材不足と作業の属人化により、
担当者がいないと作業が止まっていた - 成形日報は多いときで20枚以上/日あり、
入力に時間を取られ、ミスも起こっていた - DX化に向けて具体的に何をすべきか、
現場の意識共有が希薄だった
解 決
- 仕様書に準じて自動入力を進められるので、
担当者不在時でもバックアップが可能 - 自動化によって効率化とミス削減につながり、
ジャストインタイムの生産に貢献 - 成形日報が良い社内事例となって、
皆のやりたいDX化が明確化
導入の背景と経緯
人材不足と属人化による作業日報の問題点が顕在化。
納期の遅れや作業の漏れにつながることも。
納期の遅れや作業の漏れにつながることも。
「人材不足は製造現場のみならず、生産管理部門にも共通する課題です」と、角一化成滋賀工場次長の山倉哲郎氏は口火を切ります。「一時は半導体不足が影響した自動車産業ですが、私どもサプライヤーを取り巻く状況も回復傾向にあり、この先は1.5倍程度の受注を見込んでいます。お客様のジャストインタイム生産に応えるために、電子データを扱えるIT人材を一人でも多く確保したいところですが、なかなか厳しいのが現状です」と山倉氏。
加えて、作業の属人化も課題でした。「現場から上がってきた作業日報を、生産管理のスタッフが基幹システムに入力しますが、独自のやり方で行なうため、担当者がいないと作業がそこでストップ。納期に影響が出たり、作業に漏れがあったり、その対策を講じなければと思案していました」と振り返ります。
早速、本社に相談したところ、オムロンの業務改善サービス“pengu”の検討に至り、本社技術センターの田中健登氏をシステム導入リーダーに据えて取り組むことになりました。
「樹脂成形日報は多いときで1日20枚にもなり、それまで手入力をしていたものを、SUISUIOCRとSUISUIETLを使って自動化する仕組みづくりを行ない、業務フローを仕様書に落とし込みました。滋賀工場に提案して、各部署の皆さんの意見をまとめながら、ようやく運用に乗った段階です」と田中氏。試作開発など本来の業務で多忙な田中氏ですが、部署を超えて協力し合うことを是とする角一化成様のDX化が、こうしてスタートしました。
ココを自動化!
手入力によるデータ化・データ変換を自動化。
迅速かつミスのない基幹システムへの登録を実現。
迅速かつミスのない基幹システムへの登録を実現。
■多いときは1日20枚以上になる手書きの樹脂成形日報を、SUISUIOCRを使い、スキャンしてデータ化。
■そのデータをSUISUIETLで自動整形して、基幹システムに取り込み。
■従来は目視で手入力していた作業を自動化することで、工数削減と打ち間違い撲滅につながった。
■属人化していた作業が標準化され、担当者が不在でも別のスタッフが引き継いで作業が可能になった。
活用による効果
効率化から働き方改革、品質向上へ。
自動化による波及効果を実感。
自動化による波及効果を実感。
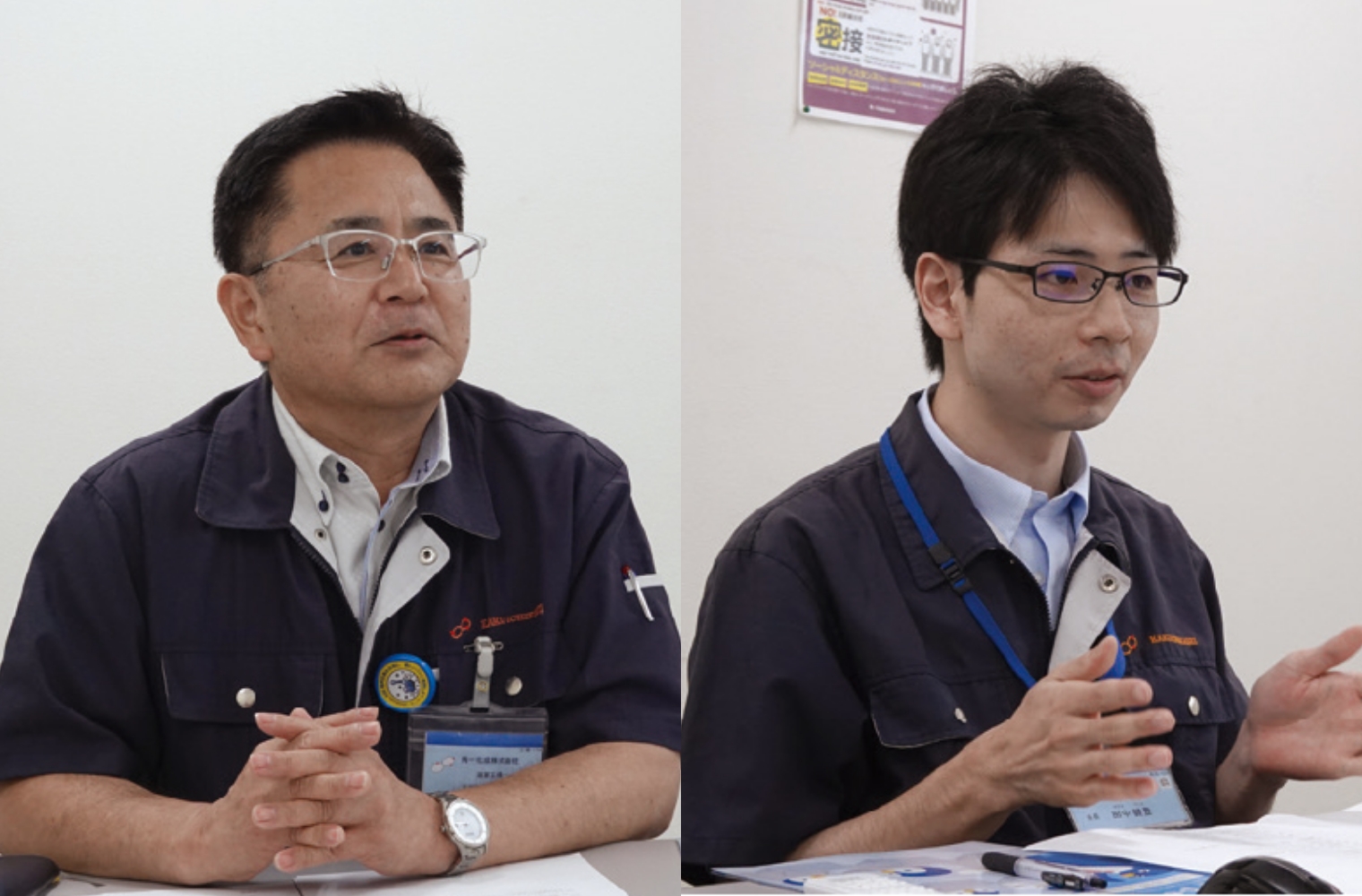
角一化成 株式会社
(左から)滋賀工場 次長 山倉 哲郎 氏、本社 技術センター 係長 田中 健登 氏
SUISUIOCRとSUISUIETLの活用により、樹脂成形日報の入力の効率化とミス削減に手応えを得た滋賀工場では現在、ゴム成形日報も自動化すべく進行中。さらに、紙帳票をスキャンした以降の作業、基幹システムへの登録までを自動化する計画を、田中氏が中心なって進めています。そこには、単に「効率化」の一言ではくくりきれない狙いもあるようです。
「作業日報は毎日欠かさずやらなくてはならないものですから、担当者にはプレッシャーがかかり、休みづらい状況がありました。その方が休むと、1日作業が滞ってしまいますから。しかし、入力作業の自動化・標準化によって、担当者が休んでも、生産管理のもう一人のスタッフが引き継げるようになりました。重責から解放されて、働き方改革のメンタルヘルス面でも良い効果が出ているのではないかと思います」と田中氏。
また、滋賀工場全体に目を配る山倉氏も「効率化」以上の効果を実感しています。「効率よくできるようになって、全体の時間を他の大事なことにも投入できるようになった意義は大きいですね。工場にはカン・コツを必要とする業務もあり、そうしたアナログで継承していくべきことにも時間を割けるようになってきています。さらに、頻繁にコミュニケーションを取ることができるようになり、品質に対する話し合いの場を持ち、そのために何をすべきか意思疎通が図れるようになりました」。
今後の展望
一つの成功事例が社員の意識を変える。
お客様に応え、そして社員のためのDX化を。
お客様に応え、そして社員のためのDX化を。
作業日報の自動化が良い社内事例となって、皆のDX化への意識が高まったいう滋賀工場。目に見える効果が、各自の業務を振り返らせたといえるでしょう。eカンバンとのデータ連携など、顧客との間でもDX化が加速する中、「発注業務、工程管理にデータ連携させれば、より動きが速くできます。従来できていないことを深掘り・合理化を図りながら、お客様に喜んでいただき、時間という付加価値を現場に生み出すシステム構築を推進していきます」と山倉氏。「まずは滋賀工場のシステム構築を急ぎ、いずれ山口工場にもカスタマイズしていく予定です。できれば各工場に1名ずつITスペシャリストを配置できれば理想的ですね」と田中氏。
製造業のフェーズが大きく変わる今、現場のDX化を推進し、お客様ニーズに応える企業様と、オムロンはpenguを通して共に走り続けてまいります。